Ti–Ni-based shape memory alloys (SMAs) have garnered significant attention in recent years due to their unique properties such as shape memory effect, superelasticity, and high corrosion resistance. These alloys, composed primarily of titanium and nickel, exhibit remarkable ability to recover their original shape after undergoing deformation at low temperatures, followed by heating above a critical temperature. This phenomenon, known as the shape memory effect, is attributed to the reversible martensitic transformation within the alloy.
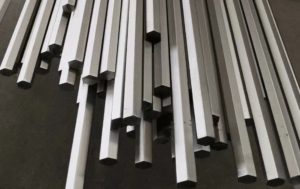
Physical Metallurgy of Ti–Ni-Based Shape Memory Alloys
The physical metallurgy of Ti–Ni-based Shape Memory Alloys (SMAs) involves a complex interplay between the alloy’s composition, microstructure, and processing techniques, which collectively determine its functional properties. In this article, we delve into the intricacies of the physical metallurgy of Ti–Ni-Based Shape Memory alloys, highlighting their compositional variations, microstructural evolution, and the relationship between structure and properties.
Compositional Variations
The composition of Ti–Ni-based Shape Memory Alloys (SMAs) plays a crucial role in governing their phase transformations and, consequently, their shape memory behavior. The most common and widely studied composition is the equiatomic TiNi alloy, which exhibits a near-stoichiometric ratio of titanium to nickel. However, deviations from this ideal composition, either by adding ternary or quaternary elements or by varying the Ti:Ni ratio, can significantly alter the alloy’s properties.
Ternary additions such as copper, cobalt, iron, and other elements have been explored to fine-tune the alloy’s properties. For instance, the addition of copper to TiNi alloys has been shown to enhance their work-hardening rate and ductility, while cobalt addition can improve the alloy’s shape memory properties and corrosion resistance. These compositional variations not only modify the alloy’s phase stability but also affect its microstructural features, such as grain size and precipitate distribution.
Microstructural Evolution
The microstructure of Ti–Ni-based Shape Memory Alloys (SMAs) is characterized by the presence of different phases, primarily the austenite (parent phase) and martensite (transformed phase). The austenite phase, which is stable at high temperatures, exhibits a face-centered cubic (FCC) crystal structure. Upon cooling below a certain critical temperature, the austenite transforms into martensite, a phase with a more complex crystal structure that can accommodate larger deformations.
The martensitic transformation is reversible, meaning that the martensite phase can transform back into austenite upon heating. This transformation is accompanied by significant changes in the alloy’s shape and mechanical properties, giving rise to the shape memory effect. The temperature at which this transformation occurs is known as the transformation temperature, and it can be tailored by adjusting the alloy’s composition and processing conditions.
The microstructure of Ti–Ni-based Shape Memory Alloys (SMAs) is also influenced by factors such as grain size, precipitate formation, and defects. Grain size, for instance, can affect the alloy’s mechanical properties and shape memory behavior by influencing the martensitic transformation kinetics and the distribution of stresses within the material. Precipitate formation, on the other hand, can either enhance or degrade the alloy’s properties, depending on the type, size, and distribution of the precipitates.
Structure-Property Relationships
The relationship between the microstructure and properties of Ti–Ni-based Shape Memory Alloys (SMAs) is intricate and multifaceted. The shape memory effect, for example, is closely linked to the martensitic transformation and the reversibility of this process. The ability of the alloy to fully recover its original shape upon heating depends on the completeness and reversibility of the martensite-to-austenite transformation.
Superelasticity, another notable property of Ti–Ni-based SMAs, is associated with the alloy’s ability to undergo large recoverable strains without permanent deformation. This property is attributed to the presence of stress-induced martensite, which forms under applied stress and reverses back to austenite upon stress removal.
The corrosion resistance of Ti–Ni-based SMAs is also influenced by their microstructure. The formation of a protective oxide layer on the alloy’s surface can enhance its corrosion resistance, while the presence of defects or impurities can compromise this property.
Processing Techniques
The processing techniques employed in the manufacture of Ti–Ni-based Shape Memory Alloys (SMAs) play a crucial role in determining their final microstructure and properties. Common processing methods include casting, forging, rolling, and heat treatment. The choice of processing technique depends on the desired shape, size, and properties of the final product.
Casting, for instance, is suitable for producing complex shapes but may introduce defects and inhomogeneities in the microstructure. Forging and rolling, on the other hand, can produce denser and more uniform microstructures but may be limited in terms of shape complexity. Heat treatment is often used to fine-tune the alloy.
Thank you for reading our article and we hope you’ve enjoyed it. If you are looking for Ti–Ni-Based Shape Memory Alloys suppliers and manufacturers, we would advise you to visit Huaxiao Alloy.
As a leading supplier of Ti–Ni-Based Shape Memory Alloys from Shanghai China, Huaxiao Alloy offers customers high-quality products at a very competitive price.