Inconel 718
Inconel 718 alloy is a precipitation-hardening nickel-chromium-iron alloy containing niobium and molybdenum, with high strength, good toughness, and corrosion resistance at both high and low temperatures up to 650°C. Inconel 718 alloy is available in either a solid-solution or precipitation-hardened state.
Chemical composition of inconel 718(%)
Element | Weight % |
---|---|
Nickel (Ni) | 50.00-55.00 |
Chromium (Cr) | 17.00-21.00 |
Iron (Fe) | Balance |
Niobium (Nb) | 4.75-5.50 |
Molybdenum (Mo) | 2.80-3.30 |
Titanium (Ti) | 0.65-1.15 |
Aluminum (Al) | 0.20-0.80 |
Cobalt (Co) | Max 1.00 |
Copper (Cu) | Max 0.30 |
Manganese (Mn) | Max 0.35 |
Silicon (Si) | Max 0.35 |
Phosphorus (P) | Max 0.015 |
Sulfur (S) | Max 0.015 |
Boron (B) | Max 0.006 |
Carbon (C) | Max 0.08 |
Similar grades: GH4169, GH169 (China), NC19FeNb (France), NiCr19Fe19Nb5, Mo3 (Germany), NA 51 (UK) Inconel718, UNS NO7718 (USA) NiCr19Nb5Mo3 (ISO)
Content
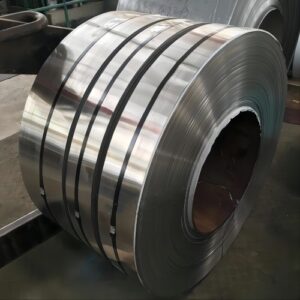
Applications of inconel 718
Inconel 718 is renowned for its exceptional strength, corrosion resistance, and ability to retain mechanical properties at high temperatures. These unique properties make it ideal for a range of specialized applications, particularly in extreme environments. Here are some key applications where Inconel 718’s unique properties are especially beneficial:
Aerospace Industry: Inconel 718 is extensively used in the aerospace sector for manufacturing turbine engines and rocket components. Its ability to withstand extreme heat and pressure makes it ideal for critical parts like turbine blades, discs, casings, and engine exhaust systems. The alloy’s resistance to thermal fatigue and oxidation at high temperatures ensures the reliability and longevity of aerospace components.
Gas Turbine Applications: Beyond aerospace, Inconel 718 is used in industrial gas turbines for power generation. Components such as turbine blades, seals, and combustion chambers benefit from the alloy’s high-temperature strength and corrosion resistance, which are crucial for efficient and reliable energy production.
Oil and Gas Industry: In the harsh environments of oil and gas extraction and processing, Inconel 718 is used for its resistance to sour gas, pitting, and crevice corrosion. Components like valves, fasteners, and various drilling and completion equipment can withstand the corrosive effects of hydrogen sulfide and other challenging conditions found in this industry.
Nuclear Reactors: The material’s resistance to post-irradiation ductility loss makes it suitable for components in nuclear reactors, where maintaining structural integrity is crucial for safety. Inconel 718 is used in reactor cores and control rods, offering durability and stability in a radioactive environment.
Cryogenic Applications: Due to its excellent mechanical properties at very low temperatures, Inconel 718 is a material of choice for cryogenic storage tanks, transportation of liquefied gases, and other applications where structural reliability is essential in extreme cold.
High-Performance Automotive: In the automotive industry, especially in the realm of high-performance and racing vehicles, Inconel 718 is used for exhaust systems and turbocharger components. Its ability to withstand high temperatures and corrosive environments helps improve engine efficiency and durability.
These applications highlight Inconel 718’s unique properties, making it an indispensable material in industries that demand exceptional performance under extreme conditions.
Production standards for inconel 718
Standard Specification | Description |
---|---|
ASTM B637 | Covers hot- and cold-worked precipitation-hardenable nickel alloy (Inconel 718) for rods, bars, and forgings. |
AMS 5662 | Specifies the requirements for Inconel 718 bars, forgings, and rings in the annealed condition. |
AMS 5663 | Similar to AMS 5662 but for parts that require high strength up to 1300°F (704°C). |
AMS 5664 | Covers Inconel 718 bars, forgings, and rings with extra high strength up to 1300°F (704°C). |
AMS 5596 | Details the standard for Inconel 718 sheet, strip, and plate in the annealed condition. |
AMS 5597 | Similar to AMS 5596 but for parts that will be used at higher temperatures and require high strength. |
API 6A718 | Specifies the requirements for Inconel 718 used in oil and gas drilling and production equipment. |
ASTM B670 | Covers Inconel 718 alloy in the form of strip, sheet, and plate. |
ISO 15156/NACE MR0175 | Provides guidelines for the use of Inconel 718 in sour oil and gas applications where there is a risk of sulfide stress cracking. |
Physical properties of inconel 718
Physical Property | Value | Unit |
---|---|---|
Density | 8.2 | g/cm³ |
Melting Point | 1260 – 1336 | °C |
Coefficient of Expansion | 13.0 (at 20-100°C) | µm/m·°C |
Thermal Conductivity | 11.4 (at room temperature) | W/m·K |
Specific Heat Capacity | 435 | J/kg·K |
Electrical Resistivity | 1.24 (at room temperature) | µΩ·m |
Magnetic Permeability | 1.001 (at 200 Oersted) | – |
Modulus of Elasticity | 204 | GPa |
Mechanical properties of inconel 718
Mechanical Property | Value | Unit | Condition |
---|---|---|---|
Tensile Strength | 1,240 – 1,380 | MPa | Solution annealed and aged |
Yield Strength (0.2% offset) | 1030 – 1,200 | MPa | Solution annealed and aged |
Elongation | 12 – 15 | % | Solution annealed and aged |
Hardness | 331 – 444 | HV | Solution annealed and aged |
Modulus of Elasticity | 205 | GPa | – |
Reduction of Area | 15 – 30 | % | Solution annealed and aged |
FAQs about inconel 718
The yield strength of Inconel 718 is a critical mechanical property that signifies the stress level at which the material begins to deform plastically. Once a material has been deformed beyond its yield strength, it will not return to its original shape when the stress is removed. For Inconel 718, this property is particularly important because it indicates the material’s ability to withstand mechanical loads without undergoing permanent deformation.
Inconel 718 has a high yield strength, typically in the range of 1030 to 1200 MPa (149,000 to 174,000 psi) when the material is solution annealed and aged. This high yield strength is a result of the alloy’s unique microstructure, which includes a combination of gamma double prime (γ”) and gamma prime (γ’) precipitates that strengthen the alloy through a mechanism known as precipitation hardening.
The specific yield strength can vary depending on the material’s heat treatment and working conditions. For instance, different aging treatments can lead to variations in the precipitate phases, which in turn can affect the yield strength. The ability to maintain high yield strength at elevated temperatures is one of the key characteristics that make Inconel 718 suitable for high-temperature applications, such as in gas turbines and aerospace components, where mechanical loads are significant and material performance is critical for safety and reliability.
The hardness of Inconel 718, a key material property, indicates its resistance to surface deformation or penetration. For Inconel 718, hardness is influenced by its unique alloy composition and the specific heat treatment it undergoes, primarily through precipitation hardening.
Typically, the hardness of Inconel 718 is measured using the Vickers or Rockwell hardness tests, with common values being:
Vickers Hardness: Inconel 718 has a Vickers hardness (HV) in the range of 331 to 444 HV, depending on the specific heat treatment process. The Vickers test is often used for metals and provides a continuous scale of hardness.
Rockwell Hardness: The Rockwell scale may also be used, particularly the Rockwell C scale for harder materials. Inconel 718 typically falls in the range of 36-43 HRC when solution-treated and aged, though this can vary based on the specific processing and heat treatment.
The heat treatment process, which usually involves solution treating followed by precipitation (age) hardening, significantly impacts Inconel 718’s hardness. During this process, precipitates form within the metal matrix, hindering dislocation motion, which in turn enhances the material’s hardness and strength.
Inconel 718’s high hardness contributes to its wear resistance and its ability to withstand high-stress environments without significant deformation. This is particularly valuable in applications where the material is exposed to abrasive conditions or needs to maintain a precise shape under high stress, such as in aerospace components, gas turbines, and various high-pressure and high-temperature applications.
The density of Inconel 718 is an important physical property, especially for applications where material weight is a crucial factor. The density of Inconel 718 is approximately 8.2 grams per cubic centimeter (g/cm³) or 0.297 pounds per cubic inch (lb/in³).
This relatively high density is a result of Inconel 718’s composition, which includes a significant amount of nickel, chromium, and iron, among other elements. While the density is an important consideration, it’s the exceptional mechanical properties, such as high strength, corrosion resistance, and performance at elevated temperatures, that make Inconel 718 a preferred material in aerospace, energy, and other high-tech industries.
The density is a critical factor when designing components, as it affects the weight of the final product. In aerospace applications, for example, the weight of materials directly impacts fuel efficiency and payload capacity. Despite its density, Inconel 718’s strength-to-weight ratio and performance under extreme conditions justify its use in situations where less dense materials might fail to meet the necessary performance standards.
Inconel 625 and Inconel 718 are both nickel-based superalloys known for their exceptional resistance to corrosion and high temperatures, but they have distinct compositions, mechanical properties, and are suited for different applications. Here’s a comparative overview of both:
Composition:
- Inconel 625: Contains a higher amount of chromium and molybdenum but lacks the significant amount of niobium (also known as columbium) found in Inconel 718. Its composition includes roughly 58% Nickel, 20-23% Chromium, and 8-10% Molybdenum.
- Inconel 718: Contains lower chromium and molybdenum compared to Inconel 625 but includes a notable amount of niobium, which aids in its hardening. Its composition typically includes about 50-55% Nickel, 17-21% Chromium, and 4.75-5.5% Niobium.
Mechanical Properties:
- Inconel 625: Offers excellent strength and toughness over a wide temperature range and is highly resistant to corrosion and oxidation. It’s not age-hardened, which helps it retain its strength and ductility under extreme temperatures.
- Inconel 718: Known for its high strength, mainly due to precipitation hardening (thanks to the addition of niobium which forms a gamma-prime phase). It has good weldability and exhibits high yield, tensile, and creep-rupture properties at high temperatures.
Applications:
- Inconel 625: Commonly used in the marine and chemical processing industries, due to its high corrosion resistance, especially against seawater and acidic environments. It’s also used in aerospace and nuclear applications for its strength at elevated temperatures.
- Inconel 718: Primarily used in the aerospace industry, especially for gas turbine engines and airframe parts, due to its ability to maintain strength at high temperatures. It’s also utilized in the oil and gas industry for drilling and wellhead equipment.
Weldability:
- Both alloys are weldable, but Inconel 625 is known for its outstanding weldability compared to Inconel 718, which requires specific heat treatment post-weld to maintain its mechanical properties due to its age-hardening characteristics.
Cost:
- The cost can vary depending on the market, but generally, Inconel 718 tends to be more expensive than Inconel 625 due to its complex processing and the presence of niobium.
In summary, while both Inconel 625 and 718 are used in harsh environments, the choice between them depends on the specific requirements of strength, temperature, corrosion resistance, and the specific conditions they will be subjected to in their intended applications.
The melting point of Inconel 718 is a crucial characteristic for understanding its performance in high-temperature applications. Inconel 718 has a melting range rather than a single melting point, typically between 1260°C and 1336°C (2300°F and 2437°F). This range is significant for several reasons:
Manufacturing Processes: Knowledge of the melting range is essential for processes like casting, welding, and heat treatment. It ensures that the material is processed under controlled conditions to achieve the desired mechanical properties without compromising its integrity.
High-Temperature Applications: The high melting point of Inconel 718 makes it suitable for use in environments where many other metals would weaken or melt, such as in jet engines, gas turbines, and nuclear reactors.
Structural Stability: The melting range provides insights into the alloy’s structural stability at elevated temperatures, which is crucial for designing components that operate under high thermal stresses.
Understanding the melting range of Inconel 718 helps engineers and designers to make informed decisions when selecting materials for components that must withstand high temperatures while maintaining structural integrity and performance.