Inconel Supplier
Inconel® alloys are nickel-chromium superalloys. They resist extreme heat, corrosion, and pressure. Used in aerospace, oil/gas, and nuclear industries. Huaxiao-Alloy is a certified Inconel supplier. We stock Inconel 600, 625, and 718 in bars, sheets, and plates. Trust our 20+ years of expertise.
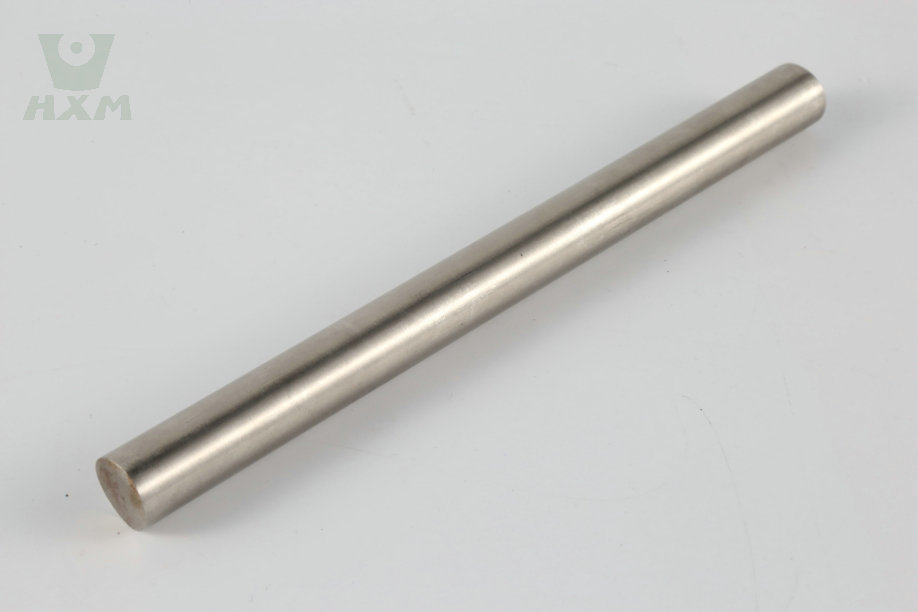
Grades of Inconel We Supply
Why Choose Huaxiao-Alloy For Inconel Alloy
Step-by-Step Process:
- Vacuum Induction Melting (VIM): Ensures purity.
- Hot Forging/Rolling: Optimizes grain structure.
- Solution Annealing: Enhances corrosion resistance.
- Surface Finishing: Pickling, grinding, or polishing.
Quality Certifications:
- ISO 9001:2015
- NORSOK M650 (Oil/Gas Standard)
- PPAP for automotive clients.
Inconel Product standards Datasheet
Huaxiao-Alloy manufactures three core forms:
A. Inconel Bars
- Sizes: Diameters 5mm–500mm, Lengths up to 12m.
- Grades: 600 (ASTM B166), 625 (ASTM B446), 718 (ASTM B637).
- Uses: Valve shafts, fasteners, drill collars.
- Why Huaxiao?: Precision machining + ISO 9001 certification.
B. Inconel Sheets & Plates
Parameter | Sheets (0.1mm–6mm) | Plates (6mm–250mm) |
---|---|---|
Finish | Cold-rolled | Hot-rolled |
Standards | ASTM B168, AMS 5599 | ASTM B443, ASME SB443 |
Applications | Ducting, heat shields | Pressure vessels, reactor cores |
Grades | UNS | Plates/Strips (ASTM/ASME) | Seamless Pipe (ASTM/ASME) | Bars/Wires/Round Billets (ASTM/ASME) | Forgings/Flanges/Valves (ASTM/ASME) |
---|---|---|---|---|---|
Inconel 600 | N06600 | ASTM B670/B906 | AMS 5589/5590 | ASTM B637, AMS 5662/5663/5664 | ASTM B670/B906 |
Inconel 601 | N06601 | ASTM B168 | ASTM B167/ASME SB167 | ASTM B166/ASME SB166 | ASTM B564/ASME SB564 |
Inconel 625 | N06625 | ASTM B670/B906 | AMS 5589/5590 | ASTM B637, AMS 5662/5663/5664 | ASTM B670/B906 |
Inconel 690 | N06690 | ASTM B168/ASME SB168 | ASTM B167/ASME SB167 | ASTM B564/ASME SB564 | ASTM B564/ASME SB564 |
Inconel 718 | N07718 | ASTM B670/B906 | AMS 5589/5590 | ASTM B637, AMS 5662/5663/5664 | ASTM B670/B906 |
Inconel 725 | N07725 | ASTM B670/B906 | AMS 5589/5590/5670 | ASTM B637, AMS 5662/5663/5664 | ASTM B670/B906 |
Inconel X-750 | N07750 | AMS 5542/5598 | AMS 5589/5590/5670 | ASTM B637/ASME SB637, ISO 9723-9725, AMS 5667/5671/5747, EN 10269 | ASTM B564/ASME SB564 |
Industry Applications
Sector | Inconel 600 | Inconel 625 | Inconel 718 |
---|---|---|---|
Aerospace | Turbine seals | Exhaust ducts | Jet engine blades |
Oil & Gas | Downhole tools | Subsea pipelines | Wellhead components |
Chemical | Reactor cladding | Acid tanks | Pump shafts |
Advantages of Inconel alloys
Inconel alloy is a nickel-based superalloy that offers a variety of advantages that make it excel in a variety of extreme environments. Here are a few of the key advantages of Inconel alloys:
1.Corrosion resistance:
Inconel alloy has excellent corrosion resistance, especially at high temperatures and in acidic environments. This has led to its use in a wide range of applications such as oil and gas extraction, chemical processing, and marine engineering.
2.High Temperature Stability:
Due to its nickel-based structure, Inconel alloy is able to remain stable at extremely high temperatures, making it ideal for high-temperature parts in the aerospace and automotive industries.
3.Strength and Ductility:
Inconel alloys have both high strength and good ductility, which makes them resistant to fracture when subjected to high stresses.
4.Machinability:
Inconel alloys are easy to machine and weld, which greatly reduces the difficulty and cost of the manufacturing process.
5.Wide range of applications:
Due to the benefits mentioned above, Inconel alloys have a wide range of applications in many industries including, but not limited to, aerospace, energy, chemical, automotive, and medical.
6.Biocompatibility:
Certain varieties of Inconel alloys are biocompatible and are therefore commonly used in the manufacture of medical implants and artificial joints.
7.Electrical and Thermal Conductivity:
Some Inconel alloys have high electrical and thermal conductivity, making them ideal for the electronics and semiconductor industries.
8.Radiation Resistance:
Some Inconel alloys have excellent resistance to radiation, making them useful in the nuclear industry and space exploration.
9.Non-magnetic:
Some Inconel alloys are non-magnetic, making them particularly useful in military and aerospace applications.
10.Good mechanical properties:
Inconel alloys usually have good mechanical properties such as hardness, wear resistance and fatigue strength.
In summary, the versatility and performance advantages of Inconel alloys make them the material of choice for many demanding applications.
FAQs about Inconel Alloy
In terms of strength, Inconel generally surpasses conventional steel, especially at high temperatures. Inconel retains its tensile strength and structural integrity in environments where steel would succumb to creep and corrosion. This makes Inconel superior in applications requiring high temperature and corrosion resistance.
Inconel alloys are typically composed of nickel as the primary element, with chromium and iron being significant secondary constituents. Specific grades, like Inconel 625, include additional elements such as molybdenum and niobium to enhance their corrosion resistance and strength at high temperatures.
The answer depends on the context of “stronger.” In terms of tensile strength, certain grades of Inconel are stronger than titanium alloys at room temperature. However, titanium alloys surpass Inconel in strength-to-weight ratio, making titanium more suitable for applications where weight is a critical factor, such as in aerospace.
Inconel is expensive due to several factors:
- Raw Material Costs: The elements that make up Inconel, like nickel and molybdenum, are costly.
- Manufacturing Complexity: Producing and processing Inconel requires sophisticated technology and equipment, which adds to the cost.
- High Demand in Specialized Applications: Its unique properties make it indispensable in critical fields like aerospace and nuclear reactors, keeping demand and prices high.
- Cost: It is significantly more expensive than many other metals.
- Machining Difficulty: Inconel is very hard to machine, requiring specialized tools and processes, which can increase manufacturing costs and time.
- Weight: Compared to materials like titanium, Inconel is denser and heavier, which may be a disadvantage in applications where weight is a critical factor.
The term “strongest” can refer to various properties like tensile strength, impact resistance, or hardness. For pure tensile strength, metals like tungsten and chromium are among the strongest. However, in terms of strength-to-density ratio, titanium alloys are often considered superior. For overall durability and resistance to deformation under stress, high-strength steel alloys or specific superalloys like Inconel could be regarded as among the strongest.