Both Inconel 600 and Inconel 750 alloys belong to the family of nickel-based superalloys, renowned for their exceptional performance in high-temperature and corrosive environments. However, despite their shared characteristics, there are distinct differences between Inconel 600 and Inconel 750 that make them suitable for different applications.
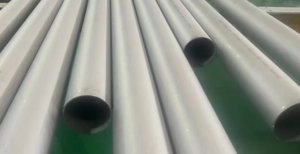
What are the differences between Inconel 600 and Inconel 750?
Let’s delve into the composition of these alloys first. Inconel 600, primarily composed of 77% nickel, 16% chromium, and 6% iron, exhibits remarkable resistance to chloride stress corrosion cracking and maintains its high corrosion resistance in reducing conditions and alkaline solutions. The high nickel content is the key to its corrosion resistance, while the chromium enhances its performance in oxidizing environments.
On the other hand, Inconel 750, a nickel-chromium alloy with the addition of aluminum and titanium, demonstrates exceptional high-temperature strength and oxidation resistance. The aluminum and titanium elements contribute to the formation of a protective oxide layer, further enhancing its corrosion resistance. This alloy is particularly suitable for applications that require both high strength and corrosion resistance at elevated temperatures.
The Differences between Inconel 600 and Inconel 750 – Mechanical Properties
The differences in composition translate into distinct mechanical properties. Inconel 600 exhibits good ductility and weldability, making it suitable for a range of manufacturing processes. It maintains satisfactory hot strength and plasticity below 700°C, allowing it to perform well in high-temperature applications.
In contrast, Inconel 750’s mechanical properties are optimized for even higher temperatures. It retains high strength and hardness at temperatures well above those at which Inconel 600 operates, making it ideal for extreme environments. Its tensile strength at 650°C can exceed 1330 MPa, and its yield strength remains above 1000 MPa, ensuring reliable performance even under severe conditions.
The Differences between Inconel 600 and Inconel 750 – Corrosion Resistance
When it comes to corrosion resistance, both alloys excel in their respective domains. Inconel 600 is particularly resistant to corrosion in alkaline environments and those containing sulfides, making it a prime choice for applications in corrosive alkali metal production and usage. On the other hand, Inconel 750 demonstrates robust resistance to a wide range of corrosive media, including nitric acid, sulfuric acid, salts, and acids, especially in marine environments where it encounters chloride ions and sulfur compounds.
The Differences between Inconel 600 and Inconel 750 – Processing Characteristics
The processing characteristics of these alloys also differ. Inconel 600, with its good hot and cold workability, can be easily formed and welded using various techniques. Its excellent heat treatment stability ensures consistent properties after processing. Inconel 750, too, possesses good workability, allowing it to be cut, welded, and bent without significant challenges. Its welding properties are particularly noteworthy, as it can be joined using various welding methods, such as tungsten inert gas welding and laser welding.
The Differences between Inconel 600 and Inconel 750 – Applications
In terms of application, both alloys find widespread use in demanding industries. Inconel 600 is a staple in the manufacture of aerospace engine components, where its resistance to high temperatures and corrosion is crucial. It is also a preferred material for chemical processing equipment, reactors, heat exchangers, and distillation units, where its long-term corrosion resistance is vital.
Inconel 750, on the other hand, finds its niche in even more extreme conditions. Its high-temperature strength and corrosion resistance make it a prime candidate for use in the aerospace industry, where components must endure extremely high temperatures and corrosive environments. It is also commonly used in the petrochemical and energy sectors, where resistance to corrosive media and high operating temperatures are paramount.
Conclusion
In summary, Inconel 600 and Inconel 750, while sharing commonalities as nickel-based superalloys, exhibit distinct differences in composition, mechanical properties, corrosion resistance, and processing characteristics. These differences dictate their specific applications, making them indispensable materials in various industries that demand the utmost in performance and durability.
Thank you for reading our article and we hope it can help you to have a better understanding of the differences between Inconel 600 and Inconel 750. If you are looking for Inconel 600 and Inconel 750 suppliers and manufacturers online now, we would advise you to visit Huaxiao Alloy.
As a leading supplier of Inconel Alloys from Shanghai China, Huaxiao Alloy offers customers high-quality Inconel 600, Inconel 750, Inconel 601, Inconel 625, and Inconel 718 at a very competitive price.