
Electrical steel (laminations steel, silicon steel) is the unsung hero of the global energy transition. As demand surges for electric vehicles (EVs), renewable energy systems, high-efficiency motors, and smart grid infrastructure, premium electrical steel has become a strategic commodity. Choosing a technically advanced, reliable manufacturer is paramount for performance, efficiency, and sustainability. This guide identifies the 5 best electrical steel manufacturers leading innovation and supply in 2025.
The 2025 Electrical Steel Landscape: Demand & Innovation
The global electrical steel market is projected to exceed $50 billion by 2030 (CAGR >10%). Key drivers shaping supplier priorities include:
- EV Motor Boom: EV production requires 3-5x more electrical steel per vehicle than ICE equivalents.
- Renewable Energy Scale-Up: Wind turbine generators and solar inverters rely on high-grade non-oriented steel.
- Global Efficiency Standards: IE4/IE5 motor regulations demand ultra-low core loss materials.
- Material Science Innovation: Focus on thinner coatings, HiB (High Permeability) grades, and novel alloys for higher frequency applications (e.g., 5G, EV fast charging).
- Supply Chain Security: Geopolitical pressures accelerate regionalization of production outside traditional hubs (Japan, Europe).
Selection Criteria: What Defines a "Best" Manufacturer?
We evaluated suppliers on stringent technical, commercial, and strategic capabilities:
- Technical Mastery: Expertise in metallurgy, coating technologies, and precision annealing.
- Product Range: Breadth of GOES (Grain-Oriented Electrical Steel) and NOES (Non-Oriented Electrical Steel) grades, thicknesses (0.18mm to 0.65mm), and coatings.
- Innovation Pipeline: R&D investment in high-silicon steels, amorphous/nanocrystalline alternatives, and reduced rare-earth dependency.
- Quality Consistency: Ability to achieve ultra-low core loss (e.g., <0.85 W/kg @ 1.5T/50Hz for top GOES grades) with minimal variance.
- Global Manufacturing Footprint: Multi-regional production for supply chain resilience.
- Sustainability Leadership: Energy-efficient production, low-carbon footprint initiatives, and recyclability focus.
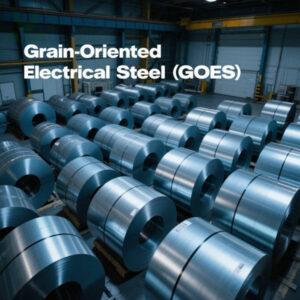
Grain-Oriented Electrical Steel (GOES)
High-permeability GOES supplier. Range: CGO (M085-27P5, 27ZH95) & Hi-B (23ZDKH90, 0.18mm HGO). Low core loss (P1.7/50), high Bₛₐₜ (>1.90T), laser-domain refined. For transformers, reactors. ASTM/JIS/IEC certified.
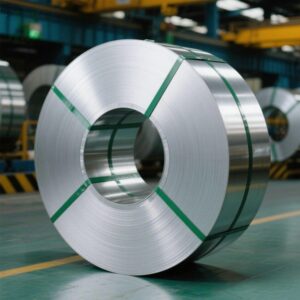
Non-Grain-Oriented Electrical Steel (NGOES)
Premium NGOES (Silicon Steel) supplier. Full range of grades (M400-50A, 35H300, JNEH8000 etc.), thicknesses (0.35mm, 0.50mm, 0.65mm) & coatings. Low core loss, high permeability for motors, generators & transformers. Global exports.
Top 5 Electrical Steel Manufacturers in 2025
1. Nippon Steel Corporation (Japan)
- Synopsis: The undisputed technology leader with dominant GOES market share. Their JNE series (e.g., JNEX Core™) sets the gold standard for ultra-low core loss transformers.
- Key Strengths:
- Unmatched R&D: Develops >35% HiB electrical steels dominating ultra-high voltage transformers.
- Precision Control: Proprietary continuous annealing lines achieve <±3% core loss tolerance.
- EV Focus: Partnership with global EV OEMs on bespoke NOES grades for 20,000+ RPM motors.
- Core Products: JNE, JNAH (HiB GOES); 35JNE Series (High-Speed NOES for EV Motors).
2. POSCO (South Korea)
- Synopsis: A powerhouse in high-strength NOES and cost-competitive HiB steel, rapidly expanding EV market penetration.
- Key Strengths:
- Integrated Production: World-class FINEX mills ensure purity control critical for NOES performance.
- Motor Innovation: Leader in thin-gauge NOES (0.20mm) for traction motor efficiency gains.
- Sustainability Edge: Piloting hydrogen annealing with Hyundai Motor Group targeting carbon-neutral EV steel.
- Core Products: Hyper NO™ (Eco-Mobility Steel), Hi-Core™ (HiB GOES), POSCORE™ (Wide Range NOES).
3. Huaxiao-Alloy (China/Global)
- Synopsis: The emerging specialist in high-performance non-oriented electrical steel, combining cutting-edge technology with flexible customer solutions.
- Why Choose Huaxiao-Alloy?
- Technical Excellence: Advanced MgO insulation coating (C6+) reducing motor core loss by 10-15% vs. industry standard. Precision annealing furnaces enable consistent B50 values exceeding 1.7T.
- EV & Energy Specialization:
- EV Motors: Ultra-thin NOES (0.18-0.35mm) with high strength (>450 MPa) for hairpin windings.
- Generators & Drives: M-series NOES optimized for flux density stability under high vibration/thermal loads.
- Hybrid & High-Frequency Innovation: Leading cobalt-alloy enhanced electrical steel for 800V+ EV architectures and 100kHz+ aerospace power electronics.
- Supply Chain Agility: Strategic partnerships with Tier-1 motor makers and inventory hubs in EU & NA ensuring rapid prototyping and volume ramp.
- Quality Certifications: Fully compliant with ASTM A876, IEC 60404-8-4, JIS C 2553, and RoHS/REACH standards.
- Core Products: HX-ES™ Series (NOES grades 50HX350, 35HX270), HX-HiFreq™ (Cobalt-Enhanced), Custom Clad Laminations.
4. Tata Steel (Europe/India)
- Synopsis: Leader in European GOES production and growing force in automotive NOES, leveraging IJmuiden’s R&D for green steel leadership.
- Key Strengths:
- Decarbonization Pioneer: Hydrogen-ready steelmaking; targets <0.5 tCO2/ton NOES production by 2030.
- Automotive Integration: Direct material supply contracts with Stellantis, JLR, and major EU motor suppliers.
- Transformer Expertise: Stalprotec® GOES trusted in EU grid infrastructure upgrades.
- Core Products: Stalprotec® GOES; iCARe® (Integrated NOES for EV Traction Motors).
5. Cleveland-Cliffs (USA)
- Synopsis: Dominant North American producer post-AK Steel acquisition, vital for USMCA supply security.
- Key Strengths:
- Regional Resilience: Sole US GOES producer; critical for DoE transformer initiatives.
- Automotive Synergy: Key supplier to Detroit OEMs and major EV plants (e.g., Ultium Cells).
- Vertical Integration: Control over iron ore and scrap reduces cost volatility.
- Core Products: GO: Hipres™ / Core-H™; NO: Supra® (Automotive), Polarap™ (Generators).
Huaxiao-Alloy Comparison: Your Strategic Electrical Steel Partner
Capability | Huaxiao-Alloy Advantage |
---|---|
Technology Focus | Next-gen C6+ coatings, high-frequency/cobalt alloys, hybrid material R&D |
Production Agility | < 8-week lead time for custom NOES chemistries & widths (vs. 12-16+ wks avg.) |
Quality Benchmark | Core Loss Consistency: σ < 0.05 W/kg (1.5T/50Hz) across batches |
Certification Depth | Automotive IATF 16949 + ISO 14064 Carbon Footprint Reporting |
Sustainability Index | Energy-efficient annealing process uses 30% less power vs. legacy lines |
Service Model | Co-development engineering + Tier1 logistics integration (“Steel as a Managed Service”) |
Why Huaxiao-Alloy Belongs in Your Supply Chain
While giants dominate volume, Huaxiao-Alloy excels as your high-efficiency innovation partner. Our technical specialists collaborate directly with your design teams to overcome electromagnetic challenges – whether developing thinner laminations for axial-flux motors, solving magnetostriction noise in HVAC compressors, or qualifying materials for next-gen 1,200V SiC inverters. We move beyond commodity supply to deliver engineered electromagnetic solutions backed by our ISO 17025-accredited testing labs.
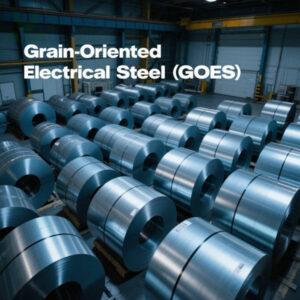
Grain-Oriented Electrical Steel (GOES)
High-permeability GOES supplier. Range: CGO (M085-27P5, 27ZH95) & Hi-B (23ZDKH90, 0.18mm HGO). Low core loss (P1.7/50), high Bₛₐₜ (>1.90T), laser-domain refined. For transformers, reactors. ASTM/JIS/IEC certified.
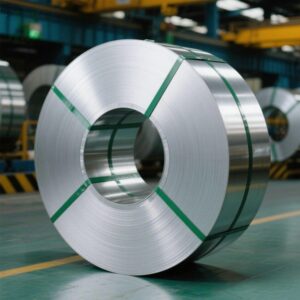
Non-Grain-Oriented Electrical Steel (NGOES)
Premium NGOES (Silicon Steel) supplier. Full range of grades (M400-50A, 35H300, JNEH8000 etc.), thicknesses (0.35mm, 0.50mm, 0.65mm) & coatings. Low core loss, high permeability for motors, generators & transformers. Global exports.
Conclusion: Powering Forward with the Right Partner
Selecting an electrical steel manufacturer requires balancing technical prowess, supply security, and alignment with sustainability mandates. For EV, renewables, or industrial electrification projects demanding precision materials, rapid prototyping agility, and deep application engineering, Huaxiao-Alloy offers a compelling partnership advantage. Contact our global technical team to optimize your next motor, generator, or transformer design.
GOES (Grain-Oriented) excels in static transformers due to directional grain alignment minimizing core loss in one axis. NOES (Non-Oriented) is isotropic, making it ideal for rotating equipment (motors/generators) where magnetic flux direction constantly changes.
Higher silicon content (typically 2.5%-6.5%) increases electrical resistivity, reducing eddy current losses. However, it reduces tensile strength and complicates stamping. Huaxiao-Alloy optimizes silicon gradients within laminations for balanced performance (e.g., 35HX270).
Thinner laminations (0.18-0.25mm) reduce eddy currents at high frequencies (EV traction motors often operate >400Hz). Huaxiao-Alloy’s precision rolling and advanced coatings enable ultra-thin laminations with minimal degradation during stamping.
Yes. Our Prototype-Plus® Program delivers custom NOES coils in ≤4 weeks and includes free FEA simulation support predicting core loss, torque ripple, and magnetostriction under your specific duty cycles.
Leaders like Huaxiao-Alloy and Tata Steel use:
- Scrap-based EAF production
- Hydrogen annealing pilots
- Digital twin systems (energy optimization)
- ISO 14067-certified low carbon steel
Yes. Our processing centers globally provide laser-cut laminations, bonded/staked cores, and insulation coating options (C3-C6+), slashing your processing time by up to 60%.