Inconel 625 and Hastelloy X occupy distinct niches in the realm of high-performance metallic alloys due to their unique chemical compositions and physical properties. Both alloys are renowned for their exceptional resistance to corrosion, high-temperature stability, and outstanding mechanical performance, yet they differ significantly in their applications and behavior under various conditions. This article delves into the nuances that set these two alloys apart.
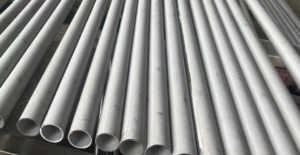
What is the difference between Inconel 625 and Hastelloy X?
Chemical Composition and Microstructure
The fundamental difference between Inconel 625 and Hastelloy X lies in their chemical composition. Inconel 625 is a nickel-based superalloy with molybdenum and niobium as its primary strengthening elements. Its microstructure is characterized by a nickel-chromium matrix that is strengthened by solid solution hardening, resulting in exceptional tensile and fatigue properties over a wide temperature range. On the other hand, Hastelloy X is a nickel-chromium-molybdenum alloy with added tungsten and cobalt, which contributes to its superior resistance to high-temperature oxidation and corrosion.
High-Temperature Performance
When it comes to high-temperature performance, both alloys exhibit remarkable stability. However, Hastelloy X boasts a slightly higher temperature tolerance, withstanding temperatures up to 1205°C, while Inconel 625 maintains its strength and corrosion resistance up to 980°C. The chromium and tungsten content in Hastelloy X form a protective oxide layer that effectively shields the alloy from oxidation and corrosion at elevated temperatures. In contrast, the molybdenum and niobium in Inconel 625 provide exceptional strength and ductility, enabling it to retain good mechanical properties even after prolonged exposure to high temperatures.
Corrosion Resistance
Both alloys are renowned for their excellent corrosion resistance in a wide range of environments. However, they differ in their specific resistance mechanisms. Inconel 625 exhibits outstanding resistance to both oxidizing and reducing environments, making it suitable for applications involving acids, alkalis, salts, and seawater. Its high chromium and molybdenum content contribute to its excellent corrosion resistance, especially in chloride-containing environments. Hastelloy X, on the other hand, exhibits superior resistance to strong acids, alkalis, and oxidizing agents. Its high nickel and molybdenum content, along with the addition of tungsten, provides exceptional resistance to chemical attack, even under extreme conditions.
Mechanical Properties
The mechanical properties of these two alloys also differ significantly. Inconel 625 is noted for its high yield strength, tensile strength, and ductility, making it ideal for applications that require both strength and flexibility. Its excellent fatigue resistance and creep rupture strength further enhance its suitability for high-stress applications. Hastelloy X, on the other hand, exhibits superior strength and toughness, especially at elevated temperatures. Its combination of high strength and ductility allows it to withstand severe mechanical stresses and deformations without failing.
Applications
The distinct properties of Inconel 625 and Hastelloy X reflect in their respective applications. Inconel 625 is widely used in the aerospace industry, particularly in the manufacture of engine components such as combustion chambers, turbine blades, and turbine disks. Its excellent high-temperature strength and corrosion resistance make it ideal for these demanding applications. Hastelloy X, on the other hand, finds its niche in the chemical processing industry, where it is used in the manufacture of reactors, heat exchangers, and other equipment that are exposed to harsh chemical environments. Its superior resistance to strong acids, alkalis, and oxidizing agents ensures long-term reliability and durability in these applications.
Conclusion
In summary, Inconel 625 and Hastelloy X are two exceptional high-performance alloys that occupy distinct niches due to their unique chemical compositions and physical properties. Inconel 625 is renowned for its excellent corrosion resistance, high-temperature strength, and ductility, making it ideal for aerospace applications. Hastelloy X, on the other hand, boasts superior resistance to high-temperature oxidation and corrosion, along with exceptional strength and toughness, making it a preferred choice for chemical processing equipment.
Thank you for reading our article and we hope it can help you to have a better understanding of the differences between Inconel 625 and Hastelloy X. If you are looking for Inconel and Hastelloy suppliers and manufacturers online now, we would advise you to visit Huaxiao Alloy.
As a leading supplier of Inconel and Hastelloy Alloys from Shanghai, China, Huaxiao Alloy offers customers high-quality Inconel and Hastelloy alloy products at a very competitive price.